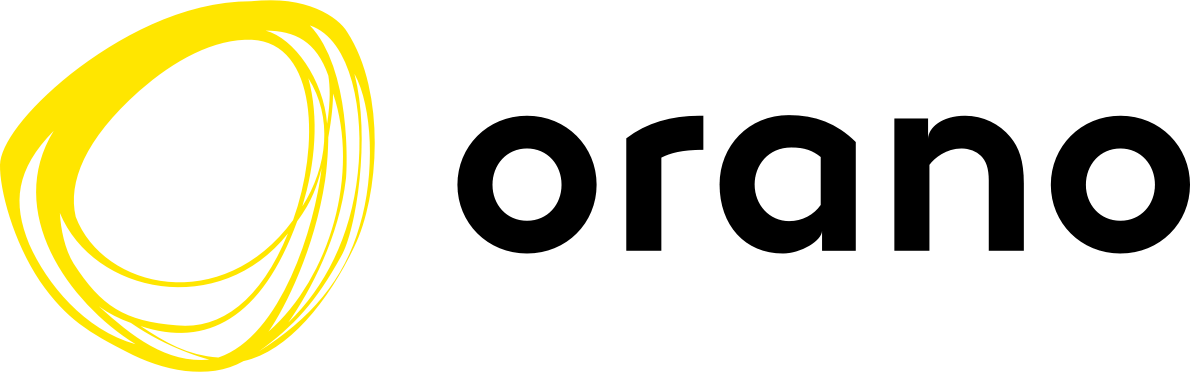
The Orano Group has invested massively over the last 15 years in the industrial platform at Tricastin to renew its production system: the Philippe Coste conversion plant was inaugurated in 2018 and the George Besse II enrichment plant in 2010. Further investment has been made to modernize the chemistry and production-support activities and to secure them over the longer term. These investments significantly strengthen the nuclear safety of the industrial operations, as they meet the most demanding standards, and limit the facilities’ environmental footprint. The new facilities thus ensure that the site’s activities can continue for the next 40 years, and contribute to France’s energy independence and to the production of low-carbon energy.
The depleted uranium obtained during the enrichment process can be converted into uranium oxide (U3O8) via the defluorination process or the denitration process. Find out more in our Uranium processing page.
The Tricastin site has unique expertise in servicing the containers used to transport uranium-bearing materials (48Y and 30B cylinders, UF4 tanks and LR65 tanks, etc.), and provides storage services for its customers.