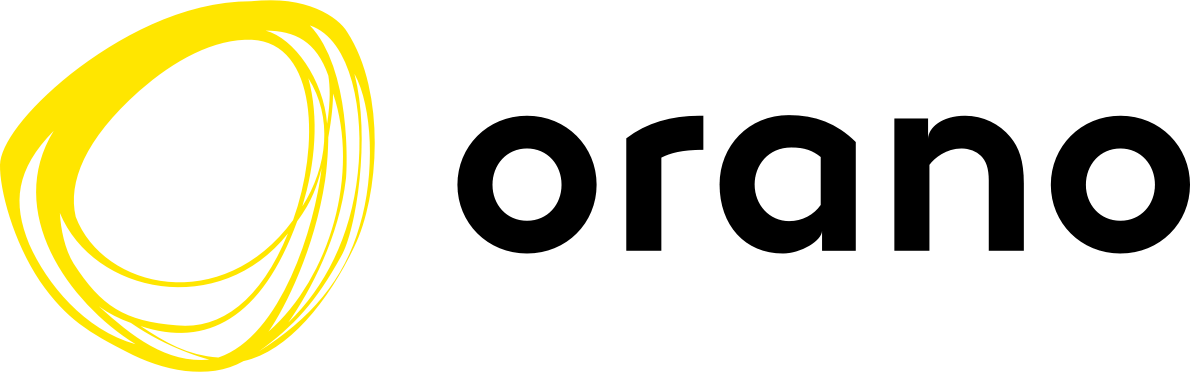
Mastering process evolutions is a key point in quality management. The SIPOC tool formally sets out all components of a process in a simple and shared manner. This approach makes it possible to describe precisely the activities of an entity, and to establish consistency between all entities, with a view to customer satisfaction.
It is of paramount importance that processes, in production as well as in the product stage, be subject to verification. This is one of the drivers of operational excellence. It defines, for each process stage, the quality criteria that will need to be verified, the related KPIs and escalation rules, with zero tolerance for deviation from the rules & criteria set.
The human factor being omnipresent, it is necessary to take it into account from the elaboration of processes, and until their implementation on the ground, in order to avoid errors generating quality problems, in particular by using the group's PFI.
The more low-level signals are captured, analysed and addressed, the more severe event occurrences decline. As there are many obstacles to the capture of weak signals, management must create the conditions for their escalation, in particular by building warning standards. Developed at each entity, the alert standard empowers teams to address the signals at the right level, and defines the escalation rules according to the severity of the event.
Sounding the alert, taking precautionary measures and reporting even before responding to an event are all essential rules of thumb. For major events, a structured problem-solving approach (A3) is initiated as a matter of standard practice, so as to pinpoint the actions to be taken, then, through standardisation, permanently record the results achieved. The non-quality cost reduction method is a continuous improvement process aimed at stepping up performance by reducing the impact of additional costs due to non-quality, solving problems and changing behaviours.These principles rely on the leadership and commitment of the entire management line.