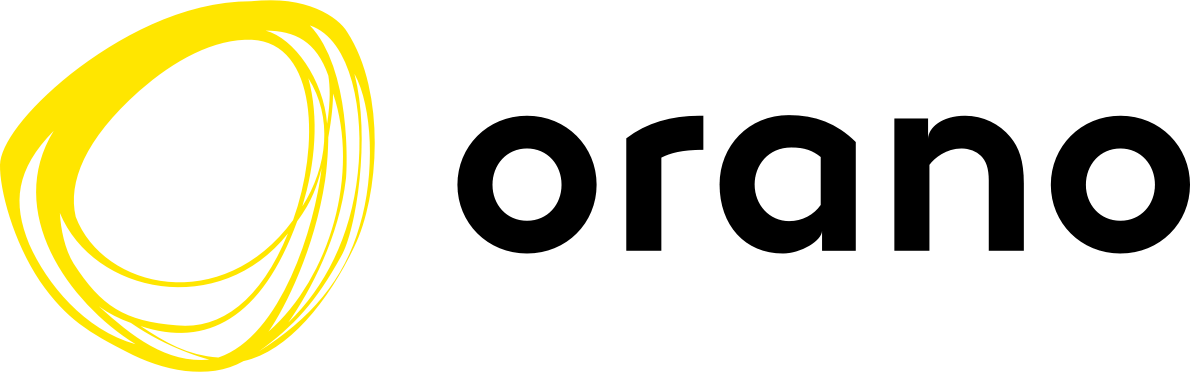
In France, the fuel cycle commences with the mining of uranium ore and culminates with the separation of recoverable, reusable materials on the one hand, and the conditioning of final waste from spent fuel on the other. One part of this cycle occurs before the reactor is loaded with fuel (the front end of the cycle) and the other occurs after the fuel is removed from the reactor (the back end of the cycle).
What are the advantages of using uranium?
Since the domestication of fire approximately 400,000 years ago, humans have utilized combustion processes to generate energy. The combustion of fuel releases energy in the form of heat. This applies to wood, gas, oil, and coal. In the case of nuclear energy, uranium is the fuel used, and the heat it releases is generated by the fission of nuclei inside the atoms (this what is known as a nuclear reaction).
Just as crude oil cannot be directly transported from the well to a car engine, uranium must undergo a transformation process before it can be loaded into a reactor.The front end of the nuclear fuel cycle encompasses four stages that must be completed before the fuel is ready for use in a reactor.
France’s uranium is mined at sites overseas, and policy measures are in place to ensure that these sites are geographically dispersed, thereby guaranteeing uninterrupted supply. The majority of uranium deposits are located in North America, Oceania, Africa, and Central Asia. Once extracted, the uranium ore must undergo crushing, milling, and processing before being concentrated. Each large rock yields only a few kilos of uranium, requiring a significant amount of material to be processed. The resulting concentrate, commonly referred to as "yellow cake," is a yellow powder produced through a combination of physical and chemical treatments.
To increase the energy yield from a given quantity of ore, it is necessary to enhance its fissility, i.e., enrich the uranium material in uranium-235. This is achieved by starting with the "conversion" stage. The conversion stage involves transforming the initial uranium concentrate into uranium hexafluoride (UF6). Various chemical treatments and processes using high-temperature ovens are used to achieve this. The resulting hexafluoride (UF6) is then transported in solid form in containers to the enrichment plant.
Uranium is enriched in uranium 235 by means of a technical process whereby UF6 is spun at very high speeds, which turns it into a gas. This "ultracentrifugation" results in an enrichment of the uranium, taking it from a natural uranium 235 content value of around 0.7% to 3 or 4%. This content is sufficient to produce fuels that are fissile (i.e., fuels that can produce more energy) when used in nuclear energy plants. 90% of the nuclear reactors currently in use in the world today run on enriched uranium.
The conversion and enrichment stages are carried out from start to finish at Orano's plants in France: at Malvési for
the first part of the conversion stage, then at Tricastin for the second part of the conversion stage (at the Philippe Coste plant)
and then for enrichment (at the Georges Besse 2 plant).
The enriched UF6, in solid form, is then moved to a fuel manufacturing plant. There, it is turned into a black powder: uranium oxide (or UO2). This powder is pressed into small cylindrical pellets ("sintering"), which
are then heated in a high-temperature oven (1,800°C). These pellets are then inserted and stacked in long tubes (4 metres long) which are made of zyrcaloy (a special alloy). These tubes or fuel rods are held together in a rigid
structure, thus forming a fuel assembly.
It takes about two years from the moment that the ore is mined to complete this fuel fabrication process. When the fuel assembly produces energy in the reactor, it loses fissile elements and gradually becomes less and less reactive. This process causes
plutonium to form and fission products appear. The assembly is designed to stay inside a reactor core for 3 to 4 years. When the assemblies become less efficient, they are unloaded from the core. Even at this point, they still contain
recoverable energy materials (uranium and plutonium). This is where the Back End of the cycle begins.
Did you know? 96% of used nuclear fuel can be recycled and reused.
In France, the back end of the fuel cycle also encompasses 4 main stages.
Once unloaded from the reactor core, the used fuel is cooled for a few months in the pools at the nuclear power plant. Once cooled, this used fuel is transferred to a treatment or reprocessing plant (the La Hague plant on France’s Cotentin peninsula, near Cherbourg). This facility is designed to recover those energy materials that remain reusable (95% uranium and 1% plutonium). This process involves mechanical procedures (the fuel is physically reduced to smaller elements) and chemical processes (the materials are dissolved and separated out using acid and solvents).
At this stage, it is possible to recycle the uranium and plutonium. The uranium output by the treatment process is still slightly enriched (0.8%). It is therefore transformed into a solid material (U308) and can stored for as long as needed. It will henceforth be available for reconversion and enrichment to be used in the manufacture of new fuels.
Plutonium also contains a tremendous amount of energy. One gram of this material can produce as much heat as one whole tonne of oil! The plutonium is also transformed into a solid (oxide) to be sent to a MOX (Mixed OXides) fuel fabrication facility. In France, this fuel production takes place at Orano's Melox plant at the Marcoule industrial platform in the Gard region (southern France).
One gram of this material can produce as much energy as one whole tonne of oil
During fuel processing operations, fission products (3% of the initial fuel) are separated out and conditioned. This material will become radioactive waste. These fission products contain almost all the radioactivity of the original fuel and they can no longer be re-used. They are melted down and mixed with a glass powder called frit and poured into a stainless steel container. Once this process, known as "vitrification”, is complete and the waste has been conditioned, it is ready to be stored in shafts at the La Hague site in France, and cooled using that site’s natural ventilation system.
While it is not the only type of radioactive waste, vitrified waste made from fission products is the most radioactive category of waste, and it is the “longest lived”. This waste is ultimately destined to be transferred to a deep geological storage facility which is currently under study (ANDRA's CIGEO project).
High-level radioactive waste represents less than 5 grams per year per capita, the equivalent of a 20 euro cent coin.”
With control over the entire fuel cycle, from uranium extraction to the reuse of recoverable materials from used fuel, France has opted for a "closed" fuel cycle. This fuel treatment-recycling strategy, mastered by Orano at its La Hague and Melox plants, has just been validated by the French government for a period extending beyond 2040.