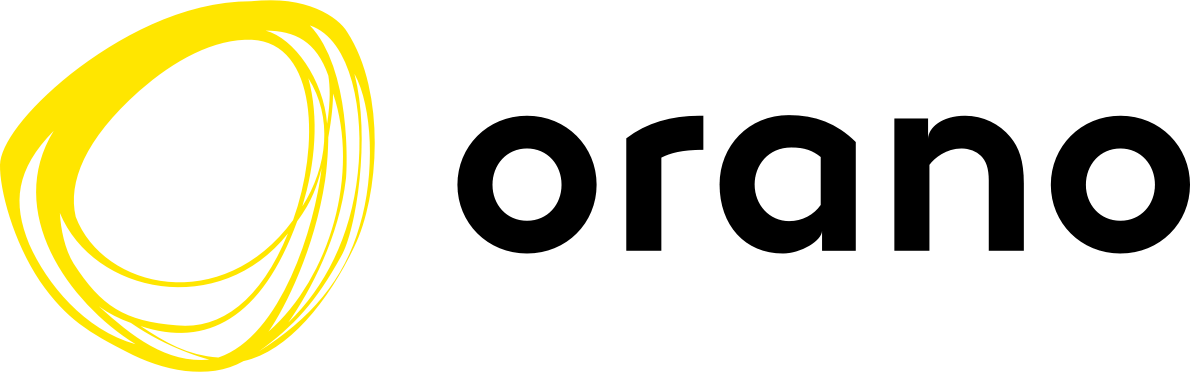
Two sites address the used fuel processing and recycling needs of electricity customers. Located about 15 miles west of Cherbourg-en-Cotentin, the site in la Hague carries out the first stage of recycling used fuel from nuclear reactors. It is the first industrial centre of its kind in the world.
Located in the Gard, the Melox site manufactures Mixed OXide (MOX) fuel assemblies designed to supply light water reactors in different countries. Melox is the world leader in this market with more than 2,600 tons produced since the start of the plant.
Orano’s technological lead has been recognized internationally for more than 40 years. Its recycling technologies are now being adopted and developed by multiple countries around the world.
La Hague has processed:
Since 1972, 44 commercial reactors worldwide have been loaded with MOX fuel, including 38 in Europe (22 in France, 10 in Germany, 3 in Switzerland, 2 in Belgium, 1 in the Netherlands).
In the Netherlands, the only nuclear power plant is operated by EPZ, a longtime client of Orano. The company chose to recycle used fuel to reduce its volume of waste. Our 360 report takes you to the Borssele site managed by EPZ, to discover a very specific nuclear waste storage building.
The “Reprocessing and Recycling” activities in la Hague are part of an agreement between Orano and EDF lasting through 2040. The volumes are defined in specific contracts. The most recent contract, signed in 2015, gives the site an unprecedented workload, with an annual production of 1,100 tons until 2022, and a significant investment in operations.
Orano is committed to operational excellence in how it serves its customers, reducing its operating costs at la Hague by 20% and strengthening product quality in its modernized, Industry 4.0-oriented plants.
Considerable investments are being made at the la Hague site to secure the long-term operability and safety of the facilities, with €1.6 billion over 8 years, or around €200 million per year.
Through recycling, up to 96% of the reuseable material in used fuel can be recovered: 1% plutonium, and 95% uranium. The remaining 4% of material are fission products, which are non-recoverable waste.
1. Safe receipt and storage of fuel prior to reprocessing
When the used fuel assemblies arrive at the la Hague site, they are first removed from their transport packaging. This operation is carried out remotely, using automated equipment in rooms with concrete walls nearly four-feet thick.
After unloading,
the fuel is kept in a storage pool for an average of five or seven years, during which time the fuel’s temperature and radioactivity naturally decreases.
4. Temporary, safe and secure interim storage pending final storage
French waste is stored at onsite at la Hague in dedicated rooms pending its transfer to the deep geological storage facility being developed through the CIGEO project.
Waste from foreign customers is returned to its country of origin as required by French law.
France’s waste amounts to 5 grams per year per inhabitant.
Mixed oxide (MOX) fuel is produced to supply nuclear power plants around the world (France, Japan, Germany). Production takes place in five stages. Depending on customer needs, the MOX fuel of plutonium and depleted uranium can contain between 3% and 12% plutonium.
The energy in a MOX assembly represents enough electricity to power a city of 100,000 inhabitants for one year.
In France, MOX produces 10% of the nuclear electricity.
Using plutonium to produce electricity for civilian use contributes to nonproliferation.
Over 130 quality parameters are used throughout the MOX production process.
Safety and security are at the heart of all of Orano's processes in la Hague and Melox. Reducing accidents to a minimum and ensuring the safety of both employees and infrastructure are the focus of constant attention at the sites. The measures taken are part of a continuous improvement approach implemented for many years.
To enable the best possible protection, nuclear facilities are structured with multiple safety barriers to ensure a total containment system for the nuclear material. Three protective barriers combine to isolate the facility with defence-in-depth strategies.
Thus, like encased Russian nesting dolls, the nuclear material is isolated in its primary confinement, enclosed within a processing room, and isolated within a secure building.
Orano's facilities continually enhance their safety policies based on industry best practices and a continuous improvement approach, in particular by strengthening the safety culture and the Organizational and Human Factors (FOH) reviews: capacities, limits and skills of agents, functioning of team work, operating procedures, constraints related to the work environment etc.
The Protection, Site and Material (PMS) service includes intervention teams trained in all the site-specific risks (chemical, fire, radioactive, etc.) with an intervention capacity equivalent to that deployed for a city of 30,000 inhabitants.
To keep safety at the highest level, the sites deploy prevention measures and regular training to reduce the likelihood of accidents, improve employee safety, and prepare staff for emergency situations through crisis exercises.
Dosimetric monitoring of process operators show radiation exposure levels well below regulatory limits.
Each day, dozens of analyses and samples are carried out in the environment to ensure that the radioactivity of products treated on the sites remains below regulatory standards.
Technically at the cutting edge when it comes to recycling used fuel and safety processing final waste products, Orano is one of world's leading industrial players.
Orano is bringing digital technologies into its fuel cycle activities. Additive manufacturing, Industrial Internet of Things (IoT), Virtual Reality and Augmented Reality have been developing in the Group for several years, serving flexibility and performance.
Orano Projets , designs and develops industrial solutions for the Group's installations and activities and for its customers.
For instance, with "Predictive Maintenance - Machine Learning", the predictive maintenance application makes it possible to track construction sites in real time by locating objects, operators, valve status, etc.
Remote operation without visual or physical access is one of the Group’s unparalleled innovations. In 2017, Orano's teams performed a complex welding operation on equipment located in a nuclear area without physical or visual access.
Equipped with computer-assisted remote operation arms and supplemented by 3D, a platform representing the R2 workshop unit was set up in the Orano Projets Research Hall for testing and training.
A complete success, the operation required 124 hours of remote operation shared by 6 employees.
In 2019, la Hague site deployed SVA (Street View Workshops) which allows one to project himself into a 360 ° and 3D environment representing the real installations. SVA provides easier and faster access to the information and helps to prepare daily or more complex interventions.
In 2019, the site introduced for the first time drones in nuclear zone to carry out visual inspections.
The ORANEF drone is equipped with an anti-collision system and a video camera. It is introduced into the nuclear zone thanks to an articulated pole. Then, it unfolds in the front cell to eventually take off. It is controlled remotely by an operator; the images are viewed online on a screen.