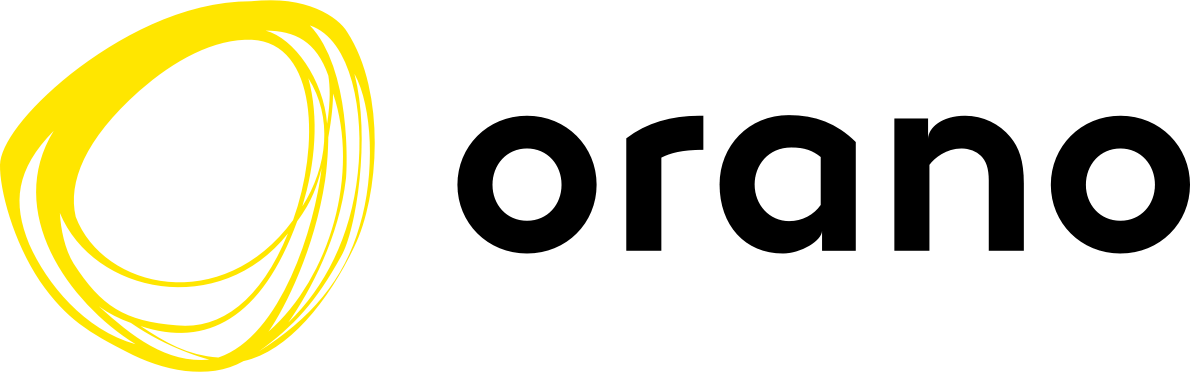
By-products from the chemical industry are generally treated as final waste. However, their composition suggests they have intrinsic value, doesn’t it?
Absolutely. It’s no secret that processing residues contain valuable by-products. For example, phosphoric acid contains elements such as vanadium and scandium, which are also found in titanium production residues. Red mud, a by-product of aluminum extraction, contains scandium and titanium. There is also uranium in phosphate deposits.
Today, these by-products are treated as waste or sometimes sold as chemical agents for other processes. That’s unfortunate because they hold significant value—especially since many of these elements are listed among the critical raw materials identified at the European level. Moreover, recovering by-products or waste aligns with environmental concerns and the principles of the circular economy.
Given the environmental stakes, recovering these by-products seems like an obvious choice. What makes CIME a key player in this market?
The SEPA and then The Innovation Center for Extractive Metallurgy (CIME) of Orano was founded over 40 years ago as part of the Orano group, building on a long-standing expertise in the development of extraction and purification processes, not only in the mining sector but also in other fields such as agri-food, healthcare, and environmental sciences.
We have state-of-the-art facilities and multidisciplinary teams capable of designing and operating pilot plants. Additionally, we have extensive expertise in hydrometallurgy, specializing in the recovery of strategic metals from processing residues and waste
By focusing on the upcycling of by-products, Orano is also addressing European supply chain security concerns regarding critical raw materials.
How does this process work in practice?
We first validate the chemistry on a small scale in our laboratory, then scale up to pilot projects to confirm the process with larger volumes. Our goal is to find the right sequence of unit operations simplifying the process as much as possible.
Our strength lies in our ability to adapt to the specifications required by our customers. By focusing on the upcycling of by-products, Orano is also addressing European supply chain security concerns regarding critical raw materials.
This also provides an opportunity to diversify into markets with high development potential. Take scandium, for example: it is used in the hydrogen sector for fuel cells, as well as in the aeronotics and automotive industries, where it enables the production of stronger and lighter alloys—ultimately reducing fuel consumption.
Vanadium, on the other hand, is primarily used in metallurgy as an alloying metal in steel and also in batteries, offering a long-lasting solution with high energy efficiency.
On paper, this approach seems promising. But in reality, where do you stand?
We are making significant progress. A key example is our flagship project, ScaVanger, which aims to develop a sustainable scandium production chain in Europe by valorizing co-products from the titanium industry.
So, are there real business prospects for the coming years?
ScaVanger et EURO-TITAN projects are sont co-financing par European Union