AUTHORSSebastien Guillot, John Mayer
Orano Decommissioning Services, LLC
PRESENTEDMarch 14, 2024
ABSTRACTOrano
DS’s patented Optimized Segmentation process was implemented for the first time at the Crystal River Unit 3 (CR3) accelerated decommissioning project in Florida. This process is an innovative approach for dismantling commercial and research nuclear
reactors to reduce the volume of waste for disposal and the amount of segmentation work on the reactor structures, which achieves substantial benefits in reducing the overall execution schedule and cost.
At CR3, using Optimized Segmentation
substantially reduced the time-consuming segmentation and packaging into numerous standardized waste containers (and multiple waste shipments) of all non-Greater-Than-Class-C (GTCC) internals and the reactor vessel. Instead, only four containers were
needed for packaging the radioactive Low-level Waste (LLW) reactor vessel and internals components.
The Optimized Segmentation process first segmented, extracted, and separated the reactor internals into two categories: 1.) GTCC waste to be
handled, packaged, and stored using conventional methods (e.g., NUHOMS® interim dry storage systems); and 2.) contaminated and activated LLW internal structures. The emptied reactor vessel was repacked using a precisely engineered placement of the
contaminated and activated waste based on each piece’s characterization. The highest LLW category components were concentrated in the middle of the vertical vessel, while less activated waste was placed in the bottom and top sections. The reactor
vessel and repackaged internals were then immobilized in hardened grout specifically prepared to immobilize the reactor internals inside the vessel and provide radiation shielding. The solid, grout-filled reactor vessel packed with waste was subsequently
segmented into three large sections (bottom, middle, top), consistent with the optimized waste distribution.
Each section was packaged and shipped individually in a tailor-made container designed to safely transport and dispose of the waste
in compliance with relevant regulations (NRC for Type B shipment, DOT for Industrial Package) and the disposal site’s Waste Acceptance Criteria. Of the three segmented reactor vessel sections, only the middle section required an NRC-approved Type
B package for shipment in accordance with 10 CFR Part 71. Orano completed the design of this Type B package in August of 2021, and the NRC Special Package Authorization to ship was issued in August 2023. The optimized waste characteristics in the two
remaining reactor vessel segments – the bottom and top sections – only required shipping containers to comply with the DOT Industrial Package regulations (49 CFR 173).
Reactor dismantling operations started at CR3 in 2021. Components
of the reactor cooling system (Steam Generators, Main Coolant Pumps & Motors, the Pressurizer, and Large Bore Piping) were removed from the containment building and shipped off site for disposal by the end of October 2021. Segmentation of the reactor
internals was conducted in 2022. Segregation, packaging, and on-site dry storage of the GTCC waste was completed in March 2023. Consolidation of the remaining internal structures into the vessel, grouting, and segmentation of the RV/RVI monolith was completed
in October 2023. All reactor segments have been packaged and stored on site in preparation for off-site shipment to the Waste Control Specialists (WCS) disposal site in Andrews, Texas, in early 2024.
INTRODUCTION - ORANO DECOMMISSIONING SERVICES AND THE CRYSTAL RIVER UNIT 3 DECONTAMINATION AND DISMANTLEMENT (D&D) PROJECT
The 860 MWe Crystal River Unit 3 Babcock and Wilcox Pressurized Water Reactor (CR3) was commissioned in 1976 and operated
for 33 years in Citrus County, Florida, until it entered its last Refueling outage in 2009 and was permanently shut down by Duke Energy in 2013. On Oct. 1, 2020, Accelerated Decommissioning Partners (ADP; a joint venture between Orano Decommissioning
Services and NorthStar Group Services) completed a transaction with CR3 owner Duke Energy to begin decontamination and dismantlement of CR3 nearly 50 years sooner than originally planned. ADP became the Nuclear Regulatory Commission-licensed operator
responsible for decommissioning the plant, and acquired the used nuclear fuel and the ISFSI assets, in compliance with all state and federal regulations.
OUR TEAM
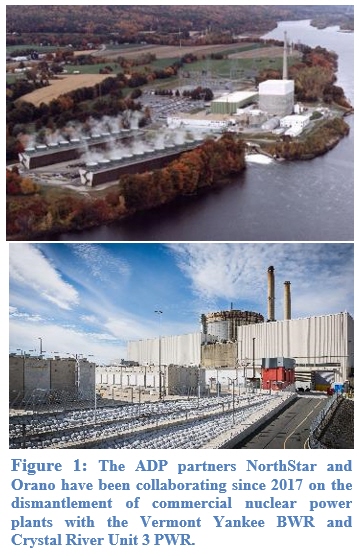
ADP was formed in 2017 between NorthStar Group Services, the largest demolition company in the world, and Orano USA. ADP delivers a unique offer adapted to best fit the needs of shutdown reactor owners and provides an accelerated turnkey
solution that completes the Nuclear Regulatory Commission license termination process for a fixed price on a guaranteed schedule.
Orano DS LLC (ODS) led a team including TN Americas (TN) and Orano Federal Services LLC (OFS) to support the CR3
dismantlement work, focused on the removal, packaging, transportation, and disposal of the Primary Cooling System large components, Reactor Vessel, and Vessel Internals.
The ADP member companies, NorthStar and Orano, completed the decommissioning
of the Vermont Yankee (VY) Boiling Water Reactor structures in December 2022, which was also the industry’s first complete and permanent license transfer of a shutdown reactor from a utility to a private entity, NorthStar, for decommissioning (Figure
1).
CONTEXT AND DRIVERS FOR INNOVATION IN REACTOR D&D - THE INCEPTION OF ORANO’S OPTIMIZED SEGMENTATION STRATEGY
Main drivers to the cost and schedule of a reactor removal operationODS has been growing its experience
and expertise in reactor D&D through the successful completion of multiple projects in Europe and the U.S., with a focus to take advantage of the state-of-the-art in all appropriate technologies, to continuously improve the reactor components segmentation
strategies and processes, and to ultimately offer solutions that reduce the cost and timeline for completion.
The main drivers in the cost and schedule of a reactor D&D operation are typically the extent of segmentation work to be performed
on the reactor components to reduce their size so they can be removed and packaged for storage, shipment, and disposal, and the number, size, and classification of the waste packages generated by the dismantling process.
The most contaminated
and activated components of a nuclear energy reactor are concentrated inside the reactor vessel (RV) and vessel internal (RVI) structures. The dismantlement of the RV and RVI structures generates the waste with the highest classifications when compared
to the rest of the radioactive waste generated during reactor dismantlement, with components classified as Class B, C, and Greater-than-Class C (GTCC), generating the highest cost for packaging, transportation, and ultimately disposal.
Optimizing
cost involves being able to segregate and distribute the generated waste within the various classifications to minimize the volume of the costliest portion of the waste, GTCC and Class B/C, balanced against the operational costs to achieve the desired
segmentation plan.
The art of planning the segmentation and packaging of the RV and RVI waste involves finding the ideal compromise working within the following constraints:
- Capabilities and limitations of the segmentation technologies available to efficiently and safely perform the separation and size reduction of highly radioactive reactor components.
- Operational costs, since the segmentation work is labor-intensive and time-consuming due to the complex environment in which the segmentation equipment is used and the highly radioactive nature of the components to be segmented.
- Capacities in weight and volume of the existing packaging systems licensed to receive and store and/or transport the generated waste in each category, driving the maximum size of the segments generated in each category. The high cost of procuring,
transporting, and disposal or storage of the waste containers encourages achieving the highest packaging efficiency, which drives towards more extensive segmentation of the reactor components.
Optimized segmentation - a safe and effective alternative to full segmentation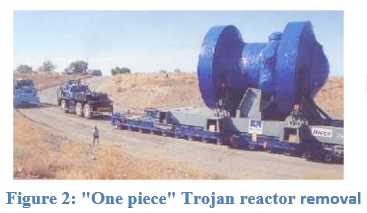
ODS’ effort to find the optimal segmentation strategy has been driven by the objective
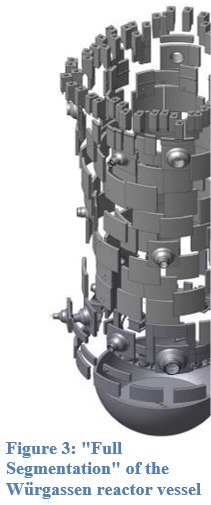
to minimize the extent of the workplan engineering,
on-site segmentation work, and the number of waste packages and shipments that typically come with the standard Full Segmentation strategy (Figure 3).
ne radical alternative to full segmentation is the “one piece” reactor removal
approach, where the entire reactor vessel is shipped, including some of the reactor vessel internals (Figure 2). This solution has been successfully implemented in previous reactor D&D projects (Trojan, Yankee Rowe, SONGS Unit 1), but involves very
large packages and conveyance systems, which will be constrained by the limitations of the available transportation route infrastructure (road and bridge capacities, and clearance limitations from other overhead structures such as bridges, tunnels, power
lines, etc.).
The “sweet spot” compromise between the “full segmentation” and “one piece” strategies resolves the challenge by accommodating the transportation logistics restrictions with custom-designed
waste containers large enough to substantially reduce the reactor component size reduction effort, while remaining transportable within existing road and transportation infrastructure capabilities.
FIRST OF A KIND SUCCESSFUL IMPLEMENTATION AT CRYSTAL RIVER UNIT 3
Crystal River Unit 3 – an advantageous set of options for off-site shipment of the waste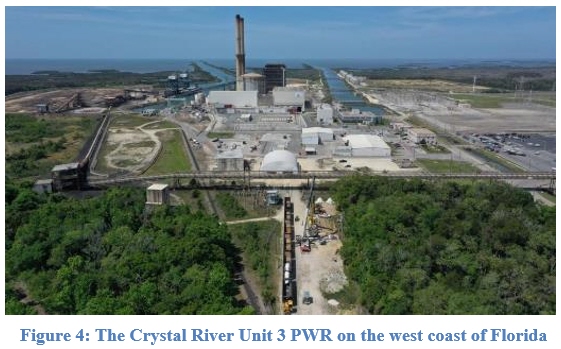
The waste generated during the D&D of CR3 (Figure 4) is
being shipped from Florida to Texas and disposed of at the Waste Control Specialists (WCS) facility in Andrews, TX. The location of CR3 offers access to transportation by road, rail, and barge through the Gulf of Mexico. The barging option offers the
opportunity to ship large containers all the way to Texas, but the transit from the eastern coast of Texas to the WCS facility in far western Texas still imposes the limitations of a long road and/or rail transportation. ODS, with support from its transportation
logistics sister division TN Americas, conducted a route survey to determine that a combination of barging and road transportation offered the opportunity to ship packages as large as 16 feet high, 20 feet wide, and with a load of up to 450,000 kilograms,
without necessitating temporary cost-prohibitive road infrastructure modifications. This envelope formed the basis of the Optimized Segmentation strategy implemented for CR3.
Optimized segmentation – a precisely engineered distribution of segmented reactor components to optimize final waste package classification, and the associated transportation and disposal costs.By modeling the operating history of the CR3 reactor, calculating and analyzing how the various components of the reactor had been irradiated and activated, and benchmarking against survey data, ODS was able to predict the expected waste classification
of each part of the RV and RVI structures.
The RV/RVI GTCC components are in the core region of the internals and consist of the core barrel and baffle assembly, the surveillance capsule holders, surveillance capsule dosimeters, and in-core
instrumentation detectors. These components have to be separated and segregated from the rest of the RV/RVI components so they can be packaged in containers that are stored onsite within the existing CR3 Independent Spent Fuel Storage Installation (ISFSI)
until a final repository is available. The RV/RVI Class B/C components are located in the other areas closest to the core region and consist of the control rod guide tube assemblies, upper core grid, the thermal shield, and lower internals assembly.
The RV/RVI Class A components are the balance of RV/RVI components, the plenum cover, plenum cylinder, core support shield assembly, reactor vessel, and vessel head.
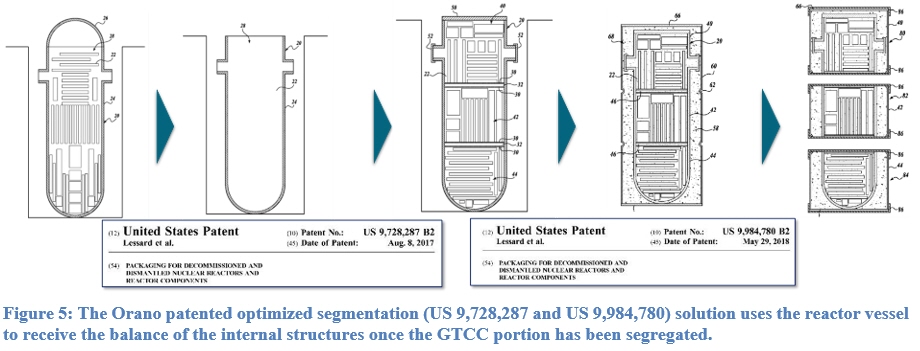
The RVI are removed from the RV, and precisely segmented underwater
using remotely operated mechanical tools to segregate the GTCC components. The optimized segmentation strategy then consists of using the reactor vessel to receive the remaining internal structures arranged in a fashion that concentrates the highest residual
activity in one area (Figure 5). The repacked RV + RVI is immobilized into a monolith by grouting, and the monolith is then segmented into three sections which can be loaded and immobilized in grout individually in large custom-designed packages. With
an optimized distribution of the activity within the RV+RVI monolith, the highest activity can be concentrated in one section and packaged into one Class B/C transportation and disposal package. The rest of the RV+RVI sections can be packaged into Class
A packages.
The CR3 optimized segmentation and packaging strategy reduces the number of containers needed to receive the reactor vessel and vessel internals segments to six. Two Rad Waste Canisters receive and store the GTCC portion of the
reactor waste in the CR3 Independent Spent Fuel Storage Installation (ISFSI). One Type B custom package is designed and licensed by the NRC to receive the RV/RVI middle section. One IP-2 metal container receives the RV/RVI top section, and Two custom-designed
and manufactured IP-2 supersacks receive the reactor head and RV/RVI bottom section.
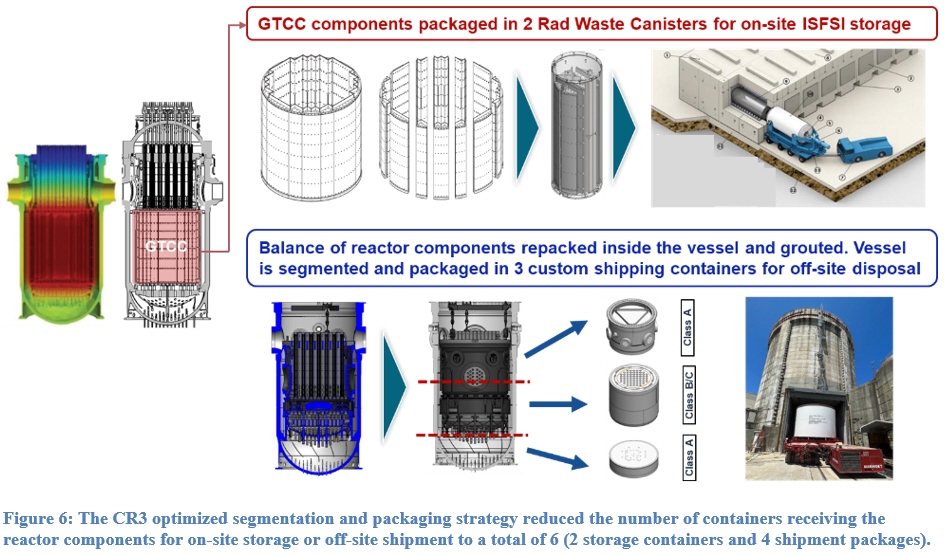
CR3 DISMANTLEMENT PROGRESS TO DATE (DECEMBER 2023)
November 2020 – October 2021: one year to prepare the site and remove the Reactor Cooling System.Upon the closure of the Crystal River Nuclear Plant Decontamination
and Dismantlement (D&D) contract between Accelerated Decommissioning Partners and Duke Energy on October 1, 2020, ODS immediately initiated its planning and site mobilization efforts.
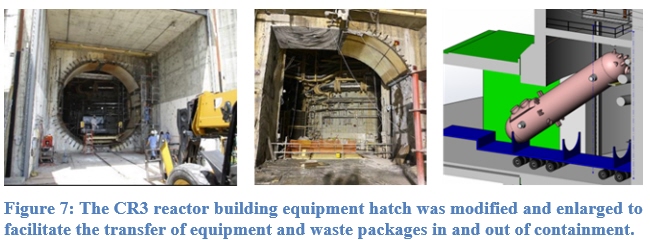
The first year of site work was focused on reactivating
and modifying the CR3 site infrastructure so it could host the D&D activities. This involved reconfiguring a facility which had been cold and dark and shut down for almost 10 years, to a fully functional and operational waste production facility,
ready to facilitate shipping a large amount of waste off-site by road, rail, and barge. This initial phase of the site work included, amongst many other activities, restoring site utilities, removing obsolete site equipment and structures, and modifying
the reactor building equipment hatch to facilitate a more efficient transfer of equipment and waste containers in and out of the building (Figure 7). The storage capacity of the existing ISFSI was extended with the addition of two horizontal storage modules
to store the GTCC waste on site with the used fuel.
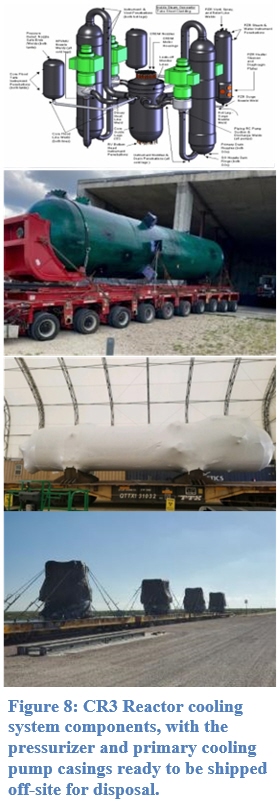
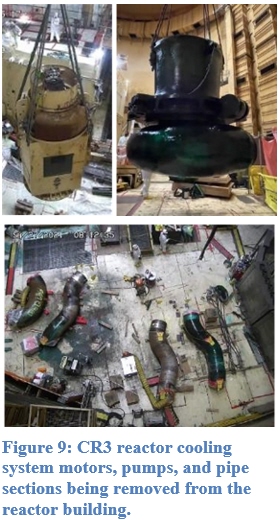
The first year was also focused on removing the reactor cooling system large components (steam generators, pumps, motors, the pressurizer, and large bore piping) from the reactor building
(Figure 8 and Figure 9), while plans and equipment procurements progressed to prepare for the reactor removal. By the end of October 2021, all large components of the cooling system were removed, packaged, shipped off-site to Texas, and disposed of at
the WCS facility.
The reactor building was then reconfigured and setup with the reactor segmentation and packaging equipment. The fuel transfer canal was cleared of all obsolete equipment, prepared with floor protection plates, deep end and
in-core instrumentation pit isolation gates, and a new working bridge with handling tools specifically designed for reactor segments was installed and commissioned. The deep end of the transfer canal was set up as an underwater segmentation workstation
with segmentation tooling and water filtration systems.
November 2021-November 2022: one year to segment the reactor vessel internals and segregate the GTCC waste.Preparations to initiate the RVI segmentation activities
were completed on December 22, 2021.
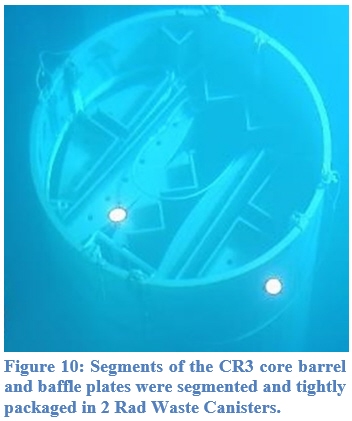
The reactor head (Figure 11) was removed from the vessel in January 2022. All control rod drive mechanisms (CRDM) were disassembled from the reactor head. The head service structure was removed from the
head and size-reduced in 3 large segments using thermal cutting. The CRDM and service structure components and segments were packaged, shipped off-site, and received and processed for disposal at the WCS site in Texas by the end of February 2022.
Work on the reactor internal structures started as soon as the reactor head was removed from the vessel and the transfer canal was flooded. The Plenum Assembly and Core Support Assembly were removed from the vessel and successively size-reduced to extract
the GTCC components and to prepare the remaining RVI structures for repositioning inside the vessel per the Optimized Segmentation plan. The underwater RVI segmentation work was completed in November 2022 with the last cuts on the core barrel.
December 2022-November 2023: one year to transfer the GTCC to dry storage, and to immobilize, segment, and package the RV/RVI components.GTCC components of the internal structures were extracted, segregated, and loaded in
liners (Figure 10) as the underwater segmentation work progressed on the Core Support Assembly. Legacy GTCC waste stored on site was added to the inventory and, by the end of December 2022, a total of 2 liners were ready to be packaged. The consolidated
GTCC waste was transferred into two Rad Waste Canisters (RWC), transferred out of the Reactor Building, and placed in dry storage in the CR3 ISFSI in January 2022.
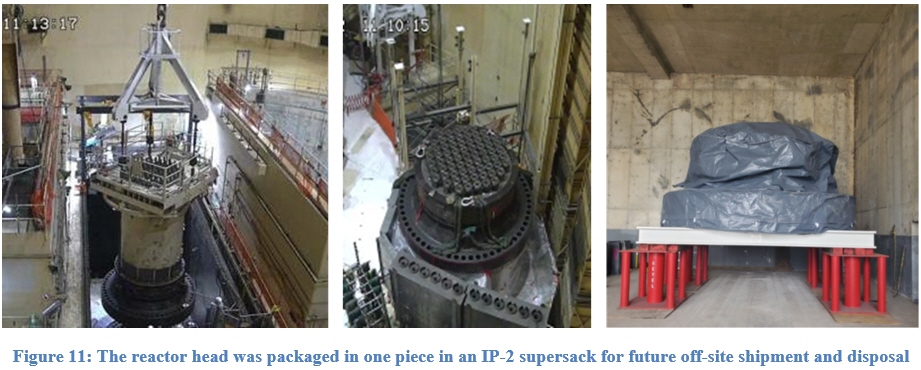
The residual vessel internals were consolidated and precisely positioned into
the empty vessel per the optimized segmentation packaging plan using purpose-designed cribbing and bracing. This enabled the final cleanup and drain down of the Fuel Transfer Canal. Overall, underwater segmentation and packaging activities on the reactor
vessel internals lasted just over a year.
The repackaged non-GTCC RVI components were then immobilized inside the vessel by injection of a designed and qualified low-density cellular concrete mix, pumped from outside the reactor building, to
form the RV+RVI monolith. The RV+RVI grouted assembly monolith was ready for final segmentation by the end of June 2023.
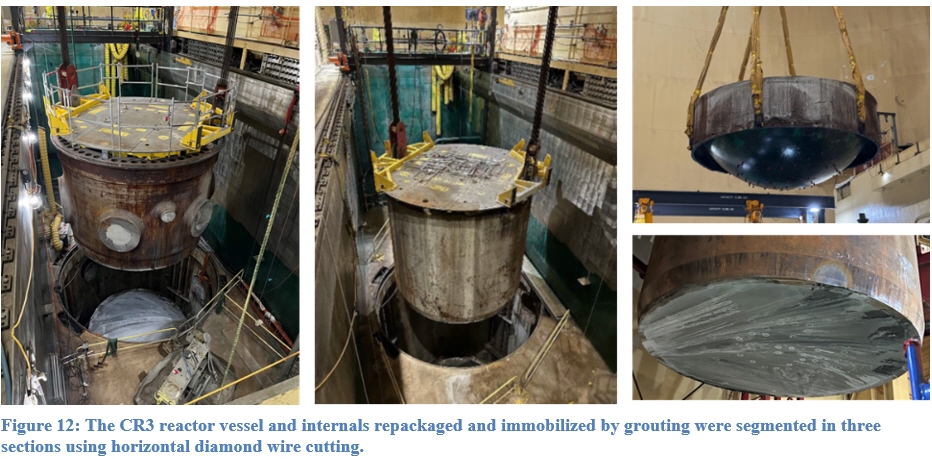
Diamond wire cutting was used to segment the RV+RVI monolith into three separate sections (Figure 12). The saws were positioned
outside the reactor cavity and on the floor of the transfer canal, and the diamond wire was guided from the saws and around the vessel outside diameter using a set of pulleys and guides mounted on a platform set on top of the vessel. This equipment was
specifically designed and extensively tested to precisely control the position of the cuts and to achieve the required flatness of the resulting cut surfaces, so each section would fit within the allocated space of the transportation packages.
The two largest reactor segments (Top and Middle sections) were lifted and transferred to purpose-designed containers in the equipment hatch area by a Heavy Lifting System specifically designed and assembled inside the reactor building to safely handle
loads up to 300,000 Kg using hydraulic strand jacks (Figure 13).
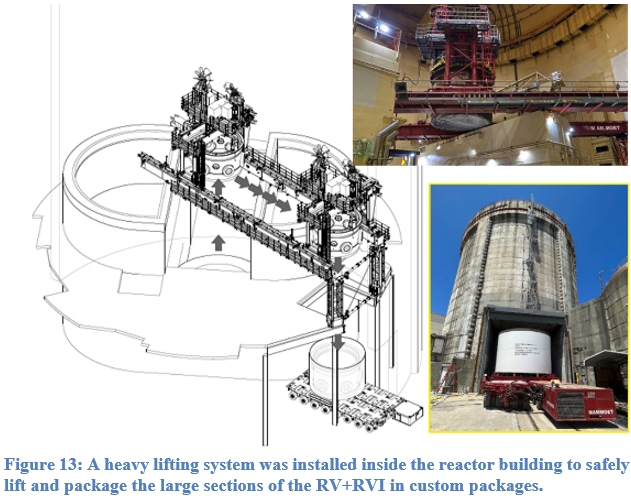
Thermal cutting was used to cut through the vessel support skirt, and the final bottom section of the reactor vessel and internals was generated, packaged into a supersack, and
transferred out of the reactor building on a purpose-built transport skid by mid-October 2023.
Operations within the reactor building completed with the cleanup of the reactor cavity and the demobilization of all equipment and staff from the
reactor building by the end of October 2023, three years after the start of the project.
CONCLUSION
In just three years since beginning the CR3 dismantling project, ODS successfully and safely completed the removal of the Reactor Vessel, Vessel Internals, and primary Cooling System Large Components by applying its patented Optimized Segmentation
strategy to simplify and accelerate the segmentation and packaging of the reactor structures, without a single lost-time accident. ODS estimates a full segmentation strategy would have required five to ten times more cuts and extended this duration by
at least a year.
All the reactor vessel and internals components have been packaged in a total of only two Class A industrial type large containers, one Class C Type B large container, and two GTCC Rad Waste Canisters (excluding the head and
the secondary waste).
This optimized packaging plan and large container strategy significantly reduced the amount of segmentation work performed on the reactor structures, accelerated progress towards their removal from the containment building,
and secured a completion of the CR3 D&D program within the six-year contract schedule.
The benefits of the Optimized Segmentation strategy include lower dose to workers during the shortened onsite operations (30 to 50%) and lower risk to
the public during the significantly reduced transportation frequency. Traditional segmentation typically requires more than 80 individual shipments of highly activated waste through the public transit system to the disposal site. Optimized segmentation
required only three shipments for the highly activated CR3 reactor components.
ODS considers Optimized Segmentation a significant evolution in decommissioning strategy that optimally reduces the risk to the worker and public, the decommissioning
fund expenditures, and the time required to achieve site release.
With its first successful implementation at CR3 completed, Orano’s Optimized Segmentation strategy is now a fully demonstrated solution available to the industry.
>> Return to Orano White Papers